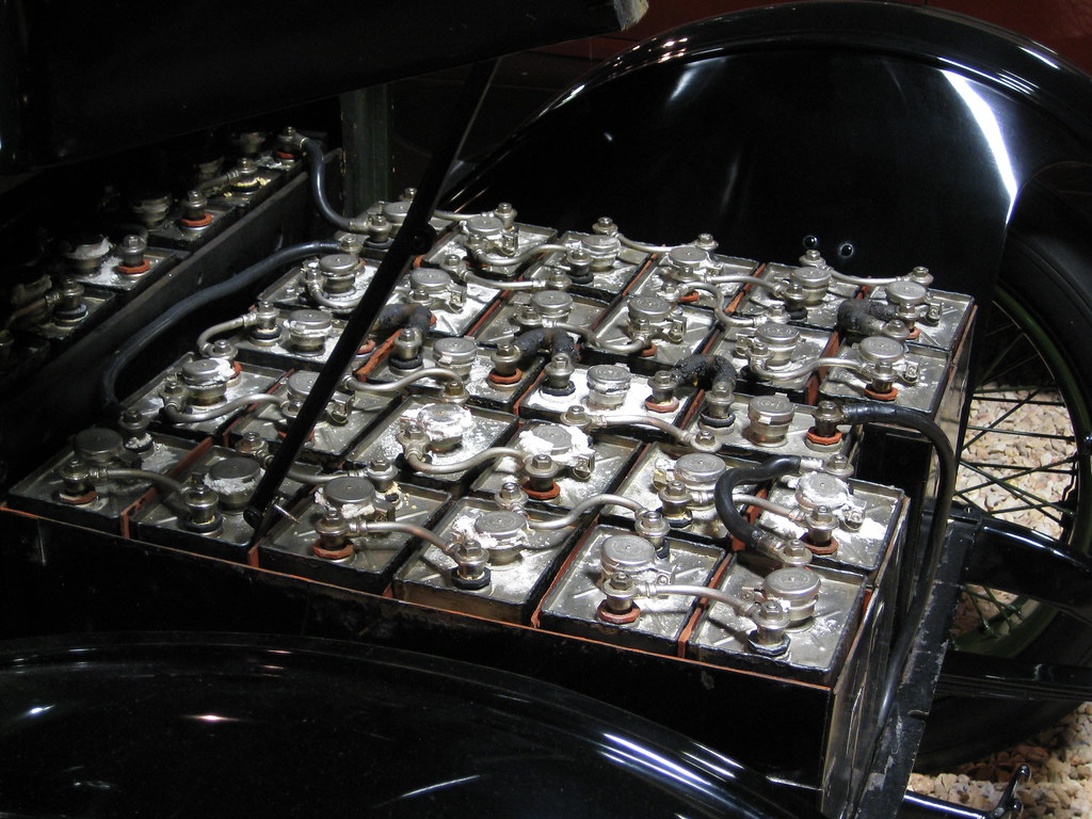
The Environmental Impact of Electric Vehicle Battery Production
Electric vehicles (EVs) are key to a greener future, but their battery production has an environmental impact. This article examines the environmental aspects of battery production, from mining raw materials to recycling, highlighting the challenges and opportunities.
Mining’s Impact: Raw Materials
Lithium-ion batteries, powering today’s EVs, require raw materials like lithium, cobalt, nickel, manganese, and graphite. Extracting these materials has environmental consequences. Lithium extraction, for instance, can use vast amounts of water, potentially leading to water scarcity and contamination, particularly in arid regions like South America’s ‘Lithium Triangle’. This area, encompassing parts of Argentina, Bolivia, and Chile, holds a significant portion of the world’s lithium reserves. Its fragile ecosystems are especially vulnerable to the impacts of water extraction used in lithium brine operations, as studies show. Cobalt presents a different challenge. It is largely mined in the Democratic Republic of Congo (DRC), where mining practices face criticism for environmental damage and human rights issues, including child labor.
Lithium Extraction: Brine vs. Hard-Rock
There are two primary methods of lithium extraction: brine extraction and hard-rock mining. Brine extraction, common in South America, involves pumping lithium-rich saltwater to the surface and allowing it to evaporate in large ponds. This method is water-intensive and can impact local water resources. Hard-rock mining, prevalent in Australia, involves extracting lithium-containing minerals from the earth. While it may use less water, it can cause habitat destruction and generate significant waste rock. The environmental impact of each method varies depending on local conditions and mining practices.
Global and Local Repercussions
Mining operations can lead to habitat loss, soil erosion, and pollution. The energy-intensive process of extracting and refining these metals contributes to carbon dioxide emissions, particularly in countries like China, where coal is still widely used. Research estimates that about two-thirds of global emissions from battery production come from China, Indonesia, and Australia.
Manufacturing’s Footprint: Energy and Emissions
Manufacturing lithium-ion batteries requires significant energy. Studies indicate that producing an EV battery can initially generate more carbon dioxide emissions than making a comparable gasoline-powered car. This is due to the high temperatures and complex chemical processes involved. As highlighted, battery production can result in up to 60% more CO2 emissions compared to making a fossil fuel car.
The Key Role of Electricity Source
The type of energy used in manufacturing is crucial. Factories powered by fossil fuels, like coal, have a much larger carbon footprint than those using renewable energy. A comparative study clearly shows how different energy sources (thermal, hydro, wind, solar, and nuclear) affect the environmental footprint, with thermal power being the most impactful.
The Impact of Battery Chemistry
The choice of battery chemistry is also important. Lithium iron phosphate (LFP) batteries generally have a lower environmental impact than nickel-manganese-cobalt (NMC) batteries. LFP batteries use abundant materials like iron and phosphate and tend to last longer. NMC batteries, while offering higher energy density, rely on scarcer materials. An impact analysis shows how shifting to LFP batteries can reduce the demand for critical metals. Studies have quantified these differences; LFP batteries have an emission intensity of approximately 55 kgCO2eq/kWh, lower than nickel-based chemistries which range around 80-82 kgCO2eq/kWh.
Advancements in Battery Technology
Research is ongoing into new battery technologies, like solid-state batteries, which could reduce environmental impact through increased energy density and lower material needs. A study indicates that solid-state batteries can reduce the carbon footprint of production by up to 39%. These use a solid ceramic material instead of liquid electrolytes.
Recycling’s Critical Role
Recycling end-of-life EV batteries is vital to reduce the need for new raw materials. However, the recycling rate for lithium-ion batteries is currently low, around 5% globally. In contrast, lead-acid batteries in gasoline-powered cars have a recycling rate near 99%. This difference, as reported, is partly because EV batteries are not designed for easy recycling.
Recycling Methods: Challenges and Solutions
There are three main methods for recycling lithium-ion batteries: pyrometallurgical, hydrometallurgical, and direct recycling. Pyrometallurgical recycling uses high heat to burn off unwanted materials and recover valuable metals, but it can be energy-intensive and produce emissions. Hydrometallurgical recycling uses chemicals to dissolve and separate metals, which can be more efficient but raises concerns about chemical waste. Direct recycling aims to recover cathode materials directly, preserving their structure and reducing the need for energy-intensive processing. This method is considered the most environmentally friendly but is still under development.
Towards a Circular Battery Economy
To minimize environmental impact, a transition to a circular economy is needed, where materials are recycled and reused. As pointed out, this requires better recycling technologies, standardized battery design, and incentives. The EU’s proposed battery regulation is a step forward, with requirements for carbon footprint declarations and increased recycling, as detailed.
Second-Life Applications for EV Batteries
Before recycling, EV batteries can often be repurposed for second-life applications. These applications, such as stationary energy storage for homes or businesses, can extend the useful life of batteries and reduce the overall environmental impact. Once a battery’s capacity has degraded to the point where it is no longer suitable for use in a vehicle, it may still retain significant storage capacity for less demanding applications. This can delay the need for recycling and provide a cost-effective energy storage solution.
Battery Swapping
Battery swapping technology offers another approach. Instead of recharging, depleted batteries are quickly exchanged for fully charged ones. This can extend battery life through more controlled charging and potentially simplify recycling. However, battery swapping requires standardization of battery packs across different vehicle models, which can be a challenge. It also necessitates a significant investment in swapping infrastructure.
The Broader Perspective: EVs and Sustainability
Despite the challenges, EVs generally have a lower environmental impact over their entire life cycle than gasoline and diesel cars, especially when charged with renewable energy. The EPA confirms that EVs typically have a smaller carbon footprint, even accounting for battery production. Japan, like the EU, is taking steps to improve transparency in EV battery production emissions, as reported.
A Multifaceted Approach
Reducing the environmental impact of EV battery production is complex and requires action on many fronts: more sustainable extraction, cleaner energy in manufacturing, improved battery chemistry, increased recycling, and a circular economy. Through innovation, policy, and a focus on sustainability, battery production can become part of a truly green transition for the transport sector.
